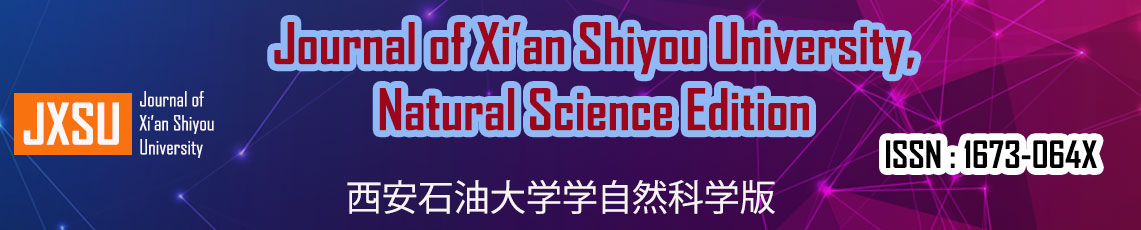
Home / Articles
Investigation of Rotating Cylinder Cooling by Multiple Cold Air Impacting Jets for Enhanced Tool Performance
This study investigates the optimization of cooling systems for cylindrical cutting tools by examining how multiple cold air jets impact a rotating cylinder, applicable to milling and grinding operations. The research employs the realizable k-ε turbulence model to analyze turbulent flow governed by Navier-Stokes equations, with numerical results validated against existing experimental data.
The study evaluates various configurations: a single nozzle at 4 diameters distance, two nozzles symmetrically arranged, three nozzles at 120° intervals, and four nozzles at 90° intervals, each tested at different Reynolds numbers. The finite volume method is used to discretize the governing equations for turbulent jet flow.
Results demonstrate that a three-nozzle configuration achieves optimal heat transfer with uniform distribution of the local Nusselt number across the cylinder's surface. This arrangement provides effective cooling while preventing thermal shock, ensuring sustained cutting tool performance during machining operations.
Index Terms- Cooling process, Rotating cylinder, Cold air impinging jets, Turbulent flow, Numerical simulation, Finite volume method, Heat transfer, Nusselt number, Tool performance, Machining operations.